4Ming press
Our revolutionary newly developed sheet metal forming machine redefines industry standards. It enables multiple deep drawing in a single tool thanks to innovative 4-drive axis technology and even allows non-cylindrical shapes to be deep drawn.
The machine is economically efficient both for flow production with a volume of 100 thousand units per year and for series production with up to 10 thousand units per year.
Several hydraulic servo axes enable a diverse range of parts. A variety of movement profiles can be run during the process, resulting in high material efficiency and robustness of the process.
One of the outstanding advantages of our machine is its free-standing design. Since no special foundation is required, installation becomes easier and more cost-effective.
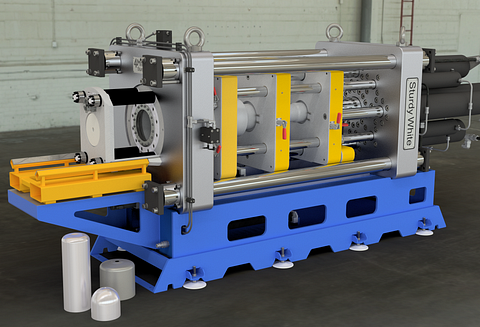
Process flow
After the board has been securely clamped, the first deep-drawing process takes place. The punch then acts as a sheet metal holder for the second draw. The diameters are gradually reduced to the final shape. Finally, secondary shapes such as holes or passages are formed.
Due to the immediate sequence of stages and the further transport of the stages on the stamps, no grippers are required, so gripper collisions are not possible. This eliminates the need for complex transport investigations.
The contact times between the punch and the material to be formed are minimal, the heat from forming remains in the material to be formed and cooling is reduced. This can mean that annealing operations can be saved when forming stainless steel.
Due to the central arrangement, there is no tilting of the ram, which would otherwise have to be taken into account and compensated for in the tool.
If products with a flange are to be manufactured, the drawn parts are not pulled completely through the drawing die. Instead, they are returned and removed in the gaps.
Parts range
The newly developed deep-drawing press, called the 4Ming ® press, produces a revolutionary variety of process combinations and thus product variants. It enables one to three times deep drawing of both the main and secondary shapes. In addition, deep drawing and ironing processes can be combined, even multiple times and in different sequences.
This combination of processes allows a variety of geometry variants to be produced. For example, a length/diameter ratio of up to 5 can be achieved without intermediate annealing. If the component is intermediate annealed, a ratio of up to 9 is possible.
The main shapes that can be produced by multiple deep drawing and ironing include draws, offset draws, prismatic main forms, non-cylindrical draws, flange draws and components with local accumulation of material in the frame or base. Components with a work-hardened base can also be produced.
Various bottom shapes can also be created, such as hemispheres, basket arches, dished bottoms, flat bottom shapes and penetration work-hardened bottoms.
The production of secondary shapes, such as perforations (with ridges inside or outside), collars on the inside or outside and hollow embossing, is also possible.
The drawn parts produced in this way are used in a variety of products. These include beverage and aerosol cans, beer barrels, gas bottles, funeral urns, fire extinguishers, oil filter housings, reflector housings, textile spools, pharmaceutical supplies and drill bits, as well as military supplies.
The 4Ming ® press is capable of processing various materials, including aluminum, steel and stainless steel. This opens up a wide range of production options and offers solutions for a wide variety of industries.
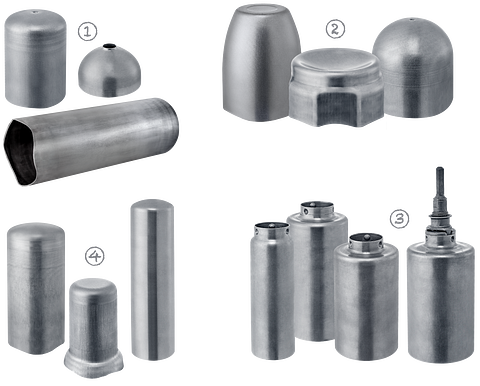
Multiple drawing enables the production of a large number of drawn part geometries. The following molds, among others, are produced on these machines today:
- Drafts pressure vessels , fire extinguishers, beer kegs, gas bottles , boilers
- Flange pulls container lids, beer kegs, gear covers
- Non-cylindrical trains air tanks , burial urns
- Detached trains Lid for container, reflector housing
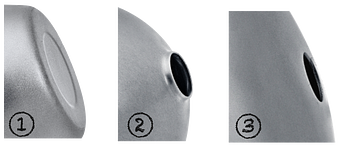
A common requirement is to create various secondary shapes on the bottom of the drawn part that have different functions:
Hollow embossing
These serve to stabilize the container and give it additional strength.
collar
Collars are used to introduce threads or to weld on fitting , for example to create a connection.
Perforations
Threaded connectors or other components can be integrated into the drawn part using holes.
The punching burr for holes can be oriented either from the inside to the outside or vice versa, depending on the application and the specific requirements.
Lorem ipsum dolor sit amet, consetetur sadipscing elitr, sed diam nonumy eirmod tempor invidunt ut labore et dolore magna aliquyam erat, sed diam voluptua. At vero eos et accusam et justo duo dolores et ea rebum. Stet clita kasd gubergren, no sea takimata sanctus est Lorem ipsum dolor sit amet.
productivity
Assuming the same press speeds, the 4Ming ® press proves to be significantly more productive. This advantage arises from the fact that there is no need for repeated setup. In addition, the loading of the blank and the removal of parts is parallelized - a process that is not possible with individual presses and press lines due to the system.
It becomes clear that the more drawing stages are carried out, the more significant the productivity advantage is.
Umformstufen | Belegungszeit Einzelpresse [s] | Belegungszeit 4Ming Presse [s] | Produktivitäts Verhältnis |
---|---|---|---|
Einstufiges Ziehen der Hauptform | 23 | 10.9 | 2.1 |
Einstufiges Ziehen der Hauptform & Nebenform | 46 | 11.9 | 3.9 |
Zweistufiges Ziehen der Hauptform & Nebenform | 67.6 | 15.4 | 4.4 |
Dreistufiges Ziehen der Hauptform & Nebenform | 88.2 | 17.8 | 5 |
Tbl. 1 Press occupancy times & productivity ratio 4Ming ® press to individual press |
Energy efficiency
The 4Ming press is remarkably energy efficient , which is due to several factors.
Firstly, during the sheet holding phase, the sheet holding cylinders do not move, which corresponds to an active counter-pulling. Therefore, the force curve for holding the sheet metal only contributes minimally to the energy balance.
Secondly, the volume of the oil column in the hydraulic cylinders at the starting point of the forming is minimal. This significantly minimizes the lossy compression volume compared to conventional hydraulic presses. The efficiency of the 4Ming press therefore reaches values of 0.6 or more.
In contrast, hydraulic individual presses require a very high removal stroke to remove the component. When the press is under load, the oil column is high, so a significant proportion of the energy has to be used for compression work. This results in a very low efficiency of 0.2.
Thirdly, thanks to the use of a variable-speed displacement control, energy is only consumed during the forming phase. This is referred to as demand-based energy supply. In contrast to classic hydraulic units for hydraulic presses, which often have a resistance control, in the 4Ming ® press there is no lossy energy conversion during standstill phases. In addition, this type of hydraulic control offers additional advantages:
- Low noise emissions
- Needs-based energy supply
- Easy integration
- Reduced installation space
- Lower tank volume due to a shortened degassing time
- No oil cooling required
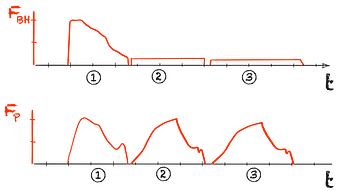
You can compare energy costs with our energy calculator. As an example, we drawing the energy costs for producing a two-pass beer keg on traditional presses with the production of the same beer keg on a 4Ming press.
As a result, it can be said that the energy costs of production on conventional hydraulic presses are €23,750 per year for a production of 100 thousand units. In contrast, the energy costs for production with the 4Ming ® press amount to just €3,630. This corresponds to a cost saving of over 80%.
Stufe | Stempel- Kraft [kN] | Niederhalter- Kraft [kN] | Mittelwert- faktor Stempel | Mittelwert- faktor Blechhalter | Wirkungs- grad | Energiekosten € |
---|---|---|---|---|---|---|
Einzelpresse Vorzug | 2,000 | 2,000 | 0.55 | 0.95 | 0.2 | 15,625 |
Einzelpresse Fertigzug | 1,500 | 500 | 0.5 | 0.95 | 0.2 | 8,125 |
4Ming Presse Vorzug | 2,000 | 2,000 | 0.55 | - | 0.6 | 1,910 |
4Ming Presse Fertigzug | 1,500 | 500 | 0.5 | - | 0.6 | 1,720 |
Tbl. 3 Energy costs per 100,000 units. / a. assuming 0.15 € / kWh |
Material efficiency
The 4Ming ® press shows remarkable material efficiency thanks to the special movement kinematics of its four actuators, which enables targeted material redistribution. This innovative process, called penetration , was developed and patented by the author in 2008.
Penetrating allows the base of the drawn part to be thinned out, allowing a smaller insert board to be used while maintaining the same length/diameter ratio. This leads to significant material savings, making the 4Ming ® press an efficient and resource-saving solution in production.484746451

A direct comparison of a penetrated beer barrel with a traditionally manufactured one shows clear differences. Particularly noteworthy is the larger flange created by the redistribution of the sheet volume from the floor. In this case, the weight of the insert board can be reduced by 370 grams. At a current daily price of €2.5 per kilogram, this results in a cost saving of €0.925 per component.
Tool change
Changing the tool in the 4Ming ® press is made efficient by an innovative system. First, the current production tool is moved to the cantilever console using linear factors. The tool is then removed using a high-lift truck and placed safely in a heavy-duty rack.
The follow-up tool is then inserted into the machine. Thanks to the recipe selection, the machine already knows the target positions of the rams. After the tool has been inserted through the actuators, all that remains is to attach the plungers to the tool stamps and the sheet metal holder using swivel clamps.
The entire tool changing process only takes about 30 minutes from good part to good part, which optimizes the production flow and minimizes downtime. This contributes to the high efficiency of the 4Ming ® press.
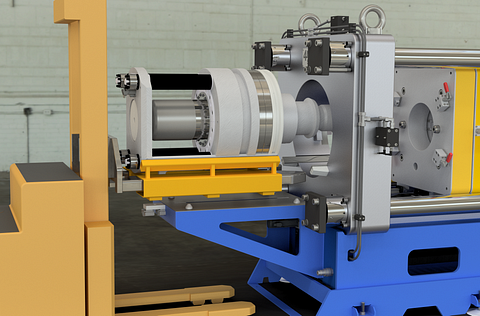
Series production
The 4Ming ® press is ideal for small and medium-sized series productions of up to 10,000 pieces per series. It offers versatile options for loading and unloading components, which can be carried out manually, automatically or by a robot.
By combining it with a trimming machine, additional edge shaping operations can be carried out subsequently, increasing production flexibility. Another key advantage is the quick tool change, which can be done from good part to good part within 30 minutes. This makes the 4Ming press an efficient tool for a wide range of manufacturing tasks and requirements.
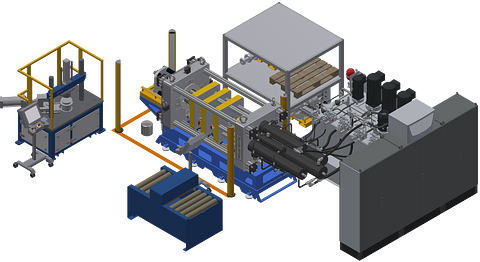
Flow production
Through the use of automation technologies and removal robots, the 4Ming press enables continuous production of several hundred thousand pieces per year. A special feature is that the stacks of circuit boards can be changed without interrupting the production process. This leads to continuous and highly efficient production, making the 4Ming press the ideal solution for large-volume manufacturing tasks.
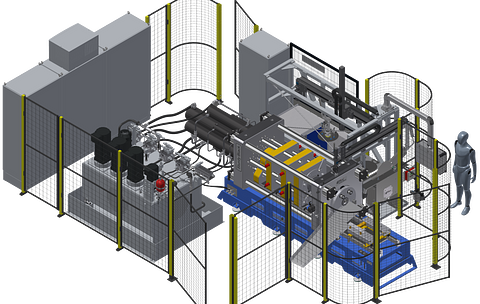
Installation examples
The 4Ming ® press has been successfully installed in many applications in the past. This manufacturing system could be successfully implemented for prototyping, small series or in flow production. Below are a few application examples:
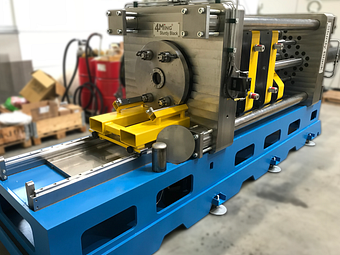
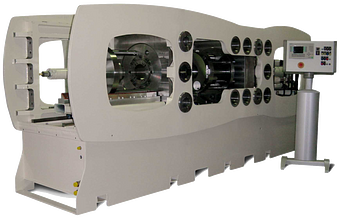
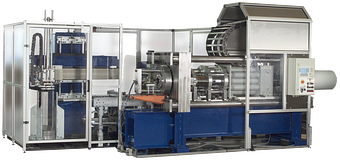
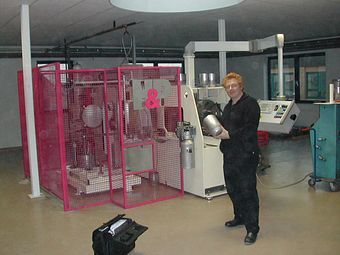
Edge processing
After the deep-drawing process, the edge processing is carried out using trimming machines. This not only allows the edge to be trimmed, but also various edge shapes, such as indentations or beads, to be formed at the same time. There is the flexibility to direct the beads either inwards or outwards. This underlines the versatile processing options and the high adaptability of the 4Ming ® press.
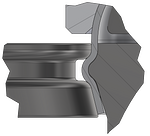
Investment comparison
In an investment comparison, the 4Ming ® press proves to be particularly economical. Compared to a single press, which requires conversion between the different work stages, the significantly higher productivity of the 4Ming ® press ensures that the additional costs are often paid off within a year.
In a comparison with a press line for beer barrels, in which several individual presses are linked through automation, it is noticeable that the investment amount for a 4Ming ® press is significantly lower than for a multi-stage press line. Therefore, the 4Ming ® press represents a cost-effective solution for companies that strive for high productivity and efficiency in their manufacturing.
Cost comparison 4Ming press and press line for slim beer barrels
Position | Pressenlinie [€] | 4Ming Presse [€] |
---|---|---|
Ziehpresse 1 | 733,000 | 700.000 |
Ziehpresse 2 | 590,000 | entfällt |
Rondenentstapelung & Befettung & Transfersystem | 534,000 | 300.000 |
Anlagen-Leitsteuerung | 56,000 | integriert |
Ziehwerkzeug 1. Zug | 112,000 | 100.000 |
Ziehwerkzeug 2. Zug | 92,000 | entfällt |
Aufstellung & Erprobung bei Hersteller | 79,000 | 79.000 |
Montage & Inbetriebnahme bei Kunden | 162,000 | 100.000 |
Fundamentkosten | 100,000 | entfällt |
Gesamtinvestition | 2,458,000 | 1.279.000 |
Tbl. 5 Cost comparison press line with 4Ming ® press for slim beer barrels |
Payback
The 4Ming ® press is characterized by its efficiency in the areas of material and energy. The savings are achieved as follows:
Material Savings: By using the 4Ming press you can save 370 grams of stainless steel per part drawn. With a stainless steel price of €2,500/ton and an annual production of 1 million drawn parts, this leads to significant material savings. The calculation showed that material savings amount to approximately €925,000 per year.
Energy Savings : The 4Ming ® press is more energy efficient than a traditional press line. The energy savings are €20,000 per 100,000 drawn parts. With an annual production of 1 million drawn parts, this corresponds to an energy saving of €200,000 per year.
Therefore, combining material and energy savings results in total savings of €1,125,000 per year. In comparison, a traditional press line would have no such savings.
Based on these annual savings, the 4Ming ® press would pay for itself in approximately 1.14 years, meaning that after this period the initial cost of the press would be offset by the savings achieved. This makes the 4Ming ® press a very cost-effective choice compared to a traditional press line.
Financing Advantage : With an interest rate of 3%, the interest payments on the 4Ming ® press over a 10-year period would be €215,370, while the interest payments on the press line would be €412,473. Therefore, using the 4Ming ® press would bring a financing advantage of €197,103 over a period of 10 years.
4Ming Presse [€] | Pressenlinie [€] | |
---|---|---|
Anschaffungskosten | 1,279,000 | 2,458,000 |
Zinszahlungen (10 Jahre) | 215,370 | 412,473 |
Gesamtkosten (Anschaffung + Zinsen) | 1,494,370 | 2,870,473 |
Tbl. 7 Financing advantage |