Tiefziehen & Abstreckgleitziehen
Es gibt bereits zahlreiche Veröffentlichungen zum Thema der Verfahrenskombination von Tiefziehen und Abstreckgleitziehen sowie zur Bedeutung dieses Prozesses in der modernen Produktionstechnologie. Als anerkannter Experte auf diesem Gebiet möchte ich in einer Reihe von Artikeln sowohl die theoretischen Aspekte als auch die praktische Anwendung dieser Techniken umfassend darstellen.
Eines der ersten Patente im Bereich Tiefziehen und Abstreckgleitziehen wurde 1904 in den USA erteilt (Patent Nr. 760, 921 von Rigby). Dennoch wurde das Verfahren bereits vor diesem Datum häufig für die Herstellung von Patronenhülsen eingesetzt.
Trotz seiner langen Geschichte liegt das Bewusstsein für die Technologie des Tiefziehens in Verbindung mit Abstreckgleitziehen und deren kommerzielle Anwendung heutzutage bei einer verhältnismäßig kleinen Gruppe von Unternehmen. Ein möglicher Grund hierfür könnte die Skepsis gegenüber diesem Prozess sein. Es ist zu hoffen, dass eine detaillierte Erläuterung dazu beitragen kann, diese Skepsis zu überwinden und ein besseres Verständnis für diese unkomplizierte Ingenieurtechnik zu schaffen.
In diesem Überblick zielt der Autor darauf ab, sowohl den akademischen Leser als auch den Leiter eines Presswerks anzusprechen.59
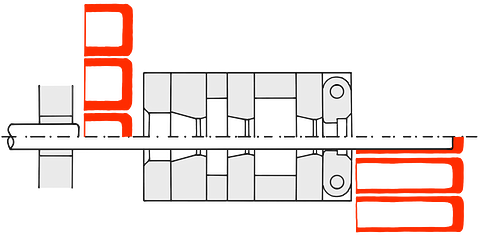
Der Prozess
Das Abstreckgleitziehen wird typischerweise an einem zylindrischen Becher mit geraden Seiten ausgeführt, der aus einer flachen Vorform durch Tiefziehen, Schmieden oder Extrudieren hergestellt werden kann. Auch das Fließpressen einer zylindrischen Vorform ist eine gebräuchliche Methode. In diesem Artikel konzentrieren wir uns jedoch auf die Herstellung aus einer kreisförmigen flachen Vorform, die stets eine größere Dicke als die endgültige Wandstärke aufweist. Dies mag offensichtlich erscheinen, doch es ist wichtig, dieses Detail zu betonen, da es sowohl Vorteile als auch Nachteile haben kann.
Wenn zum Beispiel ein Design eine besondere Dicke am Boden erfordert, wie etwa bei Patronenhülsen oder Getränkedosen, ist die dicke Vorform von Vorteil, da die Bodendicke dann der Dicke der Vorform entspricht. Bei anderen Anwendungen, wie zum Beispiel Flüssigkeits- oder Gasbehältern wie Camping-Zylindern, bei denen eine elliptische oder halbkugelförmige Endform benötigt wird, besteht kein Bedarf an überschüssigem Metall an den Enden des Behälters. In solchen Fällen wäre eine dicke Vorform eher nachteilig.
Bei der Verwendung eines dickeren Bleches sollte die Notwendigkeit eines Blechhalters hinterfragt werden. Oft ist jedoch kein Blechhalter erforderlich, was durch eine einfache Abschätzung ermittelt werden kann, wie wir sie später im theoretischen Teil dieses Artikels besprechen werden.
Bei der Arbeit mit einer Scheibe wird die Vorform am Öffnungspunkt einer Traktrix-Matrize positioniert und zentral in Bezug auf die Achse der Matrize ausgerichtet. Eine präzise Positionierung ist insbesondere bei Traktrix-Matrizen wichtig, um eine ungleichmäßige Höhe der Zarge zu verhindern. Da keine Zentrierung verwendet wird, muss die Vorform gleichmäßig in die Matrize fließen, um eine regelmäßige Form zu erzeugen.
Während des Prozesses wird die Vorform sich verdicken, wenn sie eine Becherform annimmt. Oft wird ein "korrigierendes" Abstreckgleitziehen in die Traktrix-Matrize integriert, wodurch eine gleichmäßige Wanddicke erzeugt wird, die der Dicke der ursprünglichen Vorform entspricht. Die auf die Matrize ausgeübten Radialspannungen müssen berechnet werden, und die wiederholte Radialspannung sollte hinsichtlich der Ermüdungslebensdauer berücksichtigt werden. In bestimmten Fällen kann es erforderlich sein, eine Matrize mit einer Armierung zu konstruieren.
Wenn der Prozess nicht von einer Scheibe, sondern von einer zylindrischen Vorform ausgeht, wird der Becher in einer Zentrierung positioniert und der Stempel dringt voran und führt die Bewegung in einer Führungsbuchse aus. Dieser Prozess ist in Abbildung 1 dargestellt. Das Werkstück wird in eine Senkmatrize eingebracht, die das Bauteil auf den Durchmesser des Stempels reduziert. Sobald dies erreicht ist, wird das Abstreckgleitziehen wie zuvor beschrieben ausgeführt.
Der Prozess erfordert in der Regel hydraulische Pressen mit langem Hub und speziell entwickelte Maschinen mit den entsprechenden Eigenschaften sind verfügbar. Sowohl horizontale als auch vertikale Pressen können eingesetzt werden, doch eine neue Generation horizontaler Maschinen hat den Markt betreten. Diese Pressen nutzen sowohl den Vorwärts- als auch den Rückhub effektiv. Eine detailliertere Beschreibung dieser Maschinen folgt in einem späteren Teil dieser Artikelserie.
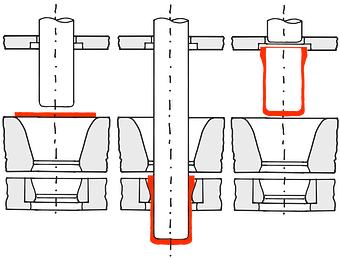
Der Abstreckgleitzieh-Prozess kann unterbrochen werden, bevor das Werkstück vollständig durch die finale Matrize geführt wird. Das Bauteil wird dann zurückgezogen und mittels einer Abstreifplatte vom Stempel gelöst, wie in Abbildung 2 dargestellt. Auf diese Weise kann ein verdickter Endabschnitt erzeugt werden, wobei die Verdickung nach Außen gerichtet ist.

Ein Stempel mit einer Änderung des Durchmessers entweder am Boden- oder am Zargenende kann ebenfalls verwendet werden, wie in Abbildung 3 dargestellt. Dies ermöglicht eine Verdickung der Innenwände des Bauteils an unterschiedlichen Stellen.
Der Prozess kann bei Bedarf sehr schnell durchgeführt werden. In solchen Fällen werden normalerweise mechanische Pressen eingesetzt. Bei der Produktion von Getränkedosen aus Aluminium oder Weißblech können Geschwindigkeiten von 150 bis 180 Hüben pro Minute mit einer einzigen Stanzpresse erzielt werden. Es gibt auch Maschinen, die zwei Stempel gleichzeitig verwenden können. Diese Methode ermöglicht die Hochgeschwindigkeitsproduktion von Patronen- oder Geschosshülsen.
Für den Prozess des Tiefziehens und Abstreckgleitziehens ist es charakteristisch, niedrige Kräfte und lange Hübe zu verwenden. Dieses Merkmal sollte mit dem Rückwärtsfließpressen aus einem Rohling oder einem Stab verglichen werden, bei dem hohe Kräfte und kurze Arbeitswege zum Einsatz kommen. In beiden Fällen wird die Fläche unter der Arbeitskurve jedoch annähernd gleich sein.
Die Stempelkraft wirkt auf den Boden des Ziehteils, was zu Zugspannungen in der Zarge führt. Wenn diese Zugspannungen die Zugfestigkeit des Materials erreichen, besteht das Risiko, dass das Bauteil bricht. Durch ein gutes Verständnis der recht einfachen beteiligten Mathematik kann eine Überbeanspruchung der Zarge des Bauteils vermieden werden.
Ohne dieses Verständnis ist es üblich, eine Reduktion der Wandstärke von 30% als bedeutend anzusehen und nach dieser Menge an Abstreckgleitziehen eine Wärmebehandlung durchzuführen. In traditionellen Branchen, wie zum Beispiel der Patronenhülsenproduktion, ist es gängig, 70/30-Messing nach etwa 30% Reduktion zu glühen. Es ist jedoch durchaus möglich, eine Reduktion von 70% bis 80% ohne Zwischenglühen zu erreichen.
Die bei starkem Abstreckgleitziehen auftretende Kaltverfestigung der Zarge muss berücksichtigt werden, da sie die endgültige Duktilität des Bauteils beeinflusst.
Warm- und Heißumformung
Die vorherige Beschreibung des Prozesses basiert auf der Durchführung bei Raumtemperatur. Allerdings können Tiefziehen und Abstreckgleitziehen auch bei erhöhten Temperaturen bis etwa 750°C (Warmumformung bei Eisenmetallen) und bis zu 1200°C (Heißumformung) durchgeführt werden.
Normalerweise wird bei höheren Temperaturen ein Rohling oder ein Stab als Ausgangsmaterial verwendet, da die notwendigen Kräfte bei diesen Temperaturen deutlich geringer sind. Durch die erhöhten Temperaturen wird die Kaltverfestigung reduziert, und größere Ziehverhältnisse sind möglich.
Bei hohen Temperaturen können Schmierung und Werkzeugverschleiß zu Problemen werden. Zudem können die Oberflächenqualität und Genauigkeit der hergestellten Teile bei der Arbeit bei Raumtemperatur überlegen sein. Es ist möglich, 70% bis 80% der Metallverformung durch Abstreckgleitziehen bei erhöhten Temperaturen zu erzielen. Der Prozess kann dann bei Raumtemperatur fortgesetzt werden, um die restlichen 20% bis 30% Verformung zu erzielen und so die Oberflächenqualität und Genauigkeit des Bauteils zu verbessern.
Die Ziehkräfte bei hohen Temperaturen können ähnlich wie bei Raumtemperatur berechnet werden. Es ist jedoch zu berücksichtigen, dass die Fließspannung des Materials und die Reibungscharakteristik bei erhöhten Temperaturen anders sein werden.
Theoretische Aspekte
Die theoretischen Aspekte von Tiefziehen und Abstreckgleitziehen sind nicht nur wichtig, sondern auch gut dokumentiert. Die Theorie des plastischen Fließens von Metallen ist seit langem Gegenstand von Untersuchungen und das Verhalten von Metallen während der Verformung wurde weitgehend erklärt.
Das theoretische Verständnis und die verschiedenen entwickelten mathematischen Formeln helfen dabei, die Vorgänge innerhalb des Werkzeugsets zu erklären und stimmen gut mit gemessenen Belastungen und anderen praktischen Faktoren überein. Dennoch wird die Theorie im Allgemeinen erst nach dem praktischen Ereignis angewandt.
Natürlich gibt es Ausnahmen. Firmen wie Liebergeld, Sieber und Schuler in Deutschland, Nobs in der Schweiz, Nords Industries, Continental Can und American Can in den USA und Metal Box in Großbritannien, um nur einige zu nennen, verfügen alle über umfangreiches Wissen über die Theorie des Prozesses. Viele andere Firmen jedoch nicht. Diese Unternehmen betonen häufig, dass sie mit ihrer Arbeit vorankommen und erfolgreich sind, und es kann gesagt werden, dass die erfahrenen Fachleute in diesen Unternehmen aus Erfahrung behaupten können, was machbar ist.
Der Autor akzeptiert diese Sichtweise, betont aber, dass dies nur eine Seite der Medaille ist. Heutzutage sind viele Dinge in der Pressewerkstatt möglich, die erfahrene Fachleute für unmöglich halten, zum Beispiel das Abstreckgleitziehen in mehr als einer Matrize gleichzeitig.
Ein weiteres Beispiel für eine gängige Überzeugung ist die Behauptung, dass es unmöglich ist, in mehr als einer Matrize gleichzeitig Abstreckgleitziehen durchzuführen. Diese Überzeugung ist weit verbreitet, obwohl sie falsch ist, und es ist oft schwierig, Menschen davon zu überzeugen, dass ein Mehrfachsystem von Matrizen funktioniert.
Diejenigen, die auf "Versuch und Irrtum" setzen, bilden wahrscheinlich das Rückgrat der Blechumformungsindustrie und stellen eine wichtige Erfahrungsbasis dar, die respektiert werden muss. Doch die Zeiten ändern sich, und mit der Weiterentwicklung von Schmierstoffen, Werkzeugmaterialien, Rohstoffen und Geräten müssen auch die Presswerke ihr Wissen anpassen und erweitern.
Ein grundlegender Aspekt beim Tiefziehen und Abstreckgleitziehen ist die Menge an Reduktion, die auftritt, wenn eine flache Scheibe in einen Becher umgewandelt wird. Es ist üblich, die Durchmesserreduktion oder das Verhältnis des Durchmessers der Scheibe zum Durchmesser des Stempels als wichtigen Parameter zu betrachten. Aber es ist genauer, das Verhältnis der Randfläche des Rohlings im Vergleich zur Randfläche der Zarge zu berechnen. Dies ist eine interessante und einfache Berechnung, die, obwohl sie bei dicken Rohlingen Fehler einführt, für dünne Rohlinge als ausreichend genau betrachtet wird.
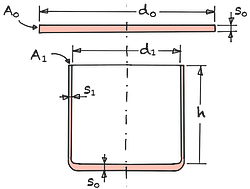
Kompression | εK | = | % |
Ziehverhältnis | βges | = | ||||
Lichte Höhe | h | = | mm | |||
Durchmesser Stempel | d1 | = | mm |
In diesem Kontext spielt die Kompression, die das Metall erfährt, eine entscheidende Rolle und ist unabhängig von ursprünglichen Parametern wie Durchmesser oder Dicke des Rohlings sowie der endgültigen Wanddicke. Als Beispiel nehmen wir an, dass das Ziehverhältnis βges = 2,2 beträgt und wir ein Ziehteil mit einem Länge-zu-Durchmesser-Verhältnis von 3:1 herstellen wollen. In diesem Fall beträgt die Kompression 85,45%.
Wenn wir das Ziehverhältnis auf 2,4 erhöhen - was sicherlich möglich ist, wenn wir eine richtig gestaltete Matrize mit Schleppkurve verwenden - sinkt die Kompression auf 83,47%. Aus Erfahrung wissen wir, dass eine Kompression von 83,5% in einem Durchgang (mit mehreren Abstreckungen) machbar ist, während 85,45% schwieriger zu erreichen sind. Daher ist die Wahl des Ziehverhältnisses äußerst wichtig.
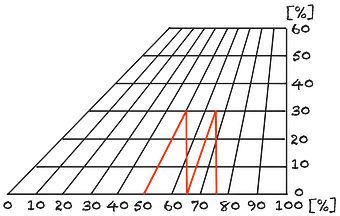
Nehmen wir als Beispiel die Herstellung eines Zylinders, bei der eine Scheibe in ein Ziehteil umgewandelt wird, bei dem der Zargenrand um 50% komprimiert ist. Gehen wir weiter davon aus, dass die nächste Abstreck-Matrize in der Sequenz eine Reduktion um 30% durchführt und die folgende Abstreck-Matrize ebenfalls eine Reduktion um 30% durchführt. Dann wissen wir, dass die Kompression εK gegeben ist durch:
(1-εK) = (1-0.5) (1-0.3) (1-0.3)
Das bedeutet, εK = 75,5%. Dies zeigt, wie die verschiedenen Reduzierungsstufen im Abstreckgleitziehen zu einer Gesamtreduktion des Metalls beitragen.
Grafisch kann dies aus Abbildung 5 ermittelt werden. Ausgehend von 50% Reduktion auf der horizontalen Achse verfolgt man die geneigte Linie bis zum Punkt, an dem die 30%-Reduktionslinie auf der horizontalen Achse erreicht wird. An diesem Punkt geht man senkrecht nach unten bis zu einer Reduktion von 65% auf der horizontalen Achse. Von diesem Punkt aus folgt man erneut der schrägen Linie, bis die 30% Reduktion erneut erreicht sind, und geht dann wieder senkrecht nach unten. Das Endergebnis ist eine Gesamtreduktion von 75,5%, die von der horizontalen Achse abgelesen wird.
Dieses Beispiel demonstriert, wie die sequenzielle Umformung in der Metallverarbeitung, speziell beim Tiefziehen und Abstreckgleitziehen, zu einer kumulativen Kompression des Metalls führt. Es verdeutlicht auch die Bedeutung der genauen Steuerung der Reduktionsstufen in jeder Phase des Prozesses, um das gewünschte Endergebnis zu erzielen.
Dieser Prozess kann, je nach Anzahl der verwendeten Matrizen, so oft wie erforderlich wiederholt werden. Insbesondere bei sehr umfangreichen Abstreckungen wird deutlich, dass der Übergang von 90% auf 95% Gesamtreduktion mindestens eine zusätzliche Matrize oder sogar mehrere erfordert, um eine weitere Kompression von 50% zu ermöglichen. Der entscheidende Punkt ist, dass die Fläche der Zylinderwände kontinuierlich abnimmt. Daher stellt eine 50%-ige Reduktion einer bereits verkleinerten Querschnittswand im Vergleich zur ursprünglichen Randfläche des Rohlings nur eine geringe Gesamtreduktion dar.
Tiefziehkraft
Die Berechnung der Stanzkraft ist beim Tiefziehen und Abstrecken von entscheidender Bedeutung. Die maximale Kraft wird während der Tiefziehphase erreicht und wenn Tractrix-Tiefziehwerkzeuge ohne Blechhalter genutzt werden, entspricht die Tiefziehkraft etwa der Hälfte der Bodenreißkraft. Aus Sicherheitsgründen empfiehlt es sich, einen Faktor von 0,6-mal der Bodenreißkraft Fzb als Tiefziehkraft anzunehmen.
Obwohl diese Berechnung einfach ist, wird oft festgestellt, dass ein echtes Verständnis für Methoden zur Bestimmung von Kräften fehlt. Ähnlich sind die Kräfte beim Rückwärtsfließpressen sehr einfach zu berechnen, werden jedoch selten in der Werkstatt angewandt. Es entsteht dann eine Situation, in der eine Presse verwendet wird, die für die Aufgabe deutlich zu groß ist, was verschwenderisch ist, oder Versuche, die Presse auf Maschinen zu nutzen, die für die Arbeit nicht stark genug sind.
Es gibt natürlich zahlreiche praktische Überlegungen. Große Pressen könnten verwendet werden, weil sie gerade ungenutzt sind, und kleine Pressen könnten aus dem gleichen Grund genutzt und dabei stark belastet werden. Dennoch ist der Autor der Meinung, dass alle Beteiligten bestrebt sein sollten, die Kluft zwischen dem versierten Praktiker und dem erfahrenen Theoretiker zu überbrücken.
Kraft beim Abstreckgleitziehen
Die Kraft beim Abstreckgleitziehen berechnet sich zu:
Die Abstreckmatrizen können so angeordnet werden, dass zwei Matrizen gleichzeitig in Aktion treten. In diesem Fall addieren sich die Presskräfte jedoch nicht einfach zusammen, sondern liegen, basierend auf empirischen Beobachtungen, deutlich darunter.
Die individuellen Kräfte werden unter der Annahme von Raumtemperaturbedingungen berechnet. Allerdings erwärmt sich das Blech während des Tiefziehprozesses und wird während der Abstrecksequenz heiß. Diese Erwärmung mildert die Kaltverfestigungseigenschaften des Stahls und erklärt hauptsächlich die beobachtete Reduzierung der gesamten Stanzlast.
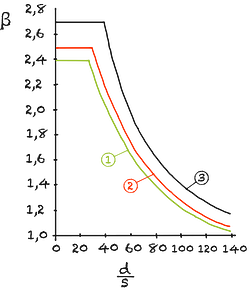
Anforderung an einen Blechhalter
Bei der Betrachtung eines dicken, starren Rohlings kann dieser selbst genug Stärke haben, um den tangentialen Druckspannungen standzuhalten, die während des Ziehvorgangs entstehen. In diesem Fall ist kein Blechhalter notwendig, und das Material kann durch eine Tractrix-Matrize gezogen werden.
Sollte die Blechdicke im Verhältnis zu ihrem Durchmesser jedoch zu gering sein, wird das Tiefziehen in einer Tractrix-Matrize ohne Blechhalter unmöglich.
Ein Blick auf Abbildung 6 zeigt, wo Instabilität auftritt, wenn kein Blechhalter genutzt wird. Diese Instabilität äußert sich in Faltenbildung oder Verwerfungen des Rohlings. Dabei hängt diese Instabilität von drei Faktoren ab: Rohlingsdurchmesser, Stempeldurchmesser und Rohlingsdicke. Diese Überlegung ist rein arithmetischer Natur und basiert auf einem flachen Stempel, der durch eine Tractrix-Matrize zieht.
In vielen Fällen sind das Ziehverhältnis oder die Dicke des Rohlings so "sicher", dass problemlos auf den Halter verzichtet werden kann. Dies gilt beispielsweise für die Herstellung von gezogenen und wandgezogenen Getränke- oder Aerosoldosen, bei denen in der Regel 0,3 mm dicke Rohlinge zum Einsatz kommen und ein Blechhalter notwendig ist, um Verwerfungen zu vermeiden.
Als einfaches Beispiel: Wird ein 0,3 mm dicker Rohling mit einem Ziehverhältnis von (sagen wir) 2:1 verwendet, kann auf einen Blechhalter verzichtet werden, solange nur ein Stempeldurchmesser von maximal etwa 10 mm genutzt wird.
Es gibt jedoch weitere Aspekte, die bei der Beurteilung der Neigung eines Rohlings zum Verwerfen oder Falten berücksichtigt werden müssen. Ist ein Rohling weder sicher noch unsicher, sollten weitere Faktoren in Betracht gezogen werden. Die Form des Stempelbodens kann ebenso einen deutlichen Einfluss auf die Tendenz zur Faltenbildung haben wie die Qualität der Rohlingskante und die Härte des Rohlings.
Befindet sich ein Rohling nahe an einem Zustand, in dem er sich verformt, kann es je nach Rohlingshärte dazu kommen, dass er sich jedes Mal verformt oder überhaupt nicht. Bei der Herstellung eines Feuerlöschergehäuses aus extra tiefziehfähigem Stahl wurde festgestellt, dass eine Härte von weniger als 100HV zu Falten führte, während bei einer Charge Stahl mit einer Härte von mehr als 120HV keine Falten auftraten.
Es wurde ebenfalls festgestellt, dass das "Ziehen an der Grenzlinie" mit einer Standard-Geometrie-Tractrix-Matrizenform zur Faltenbildung führte. Als das Matrizenprofil jedoch modifiziert wurde, um Verdickung und Dehnung des Rohlings zu berücksichtigen, wurden die Faltenprobleme sofort behoben.
Dies ist der Punkt, an dem die Kunst des Metallumformens die theoretischen Vorhersagen übertrifft und ein Bereich des
Kombination mit dem Mehrfachziehen
Bislang wurden nur Einzelziehvorgänge betrachtet, die ein maximales Länge-zu-Durchmesser-Verhältnis von 3:1 ermöglichen.
Wenn dieser Zylinder jedoch auf einem zweiten Stempel durch Mehrfachziehen nachgezogen wird, wird zusätzliches unvergütetes Metall aus dem weichen Grund des Bauteils in die Seitenwände gezogen. Ohne eine Zwischenglühung kann das Nachziehverhältnis (1. Stempel + 2. Stempel) einen Maximalwert von etwa 1,4:1 erreichen. Dadurch erhöht sich das fertige Höhe-zu-Durchmesser-Verhältnis auf etwa 4:1.
Wird jedoch eine Zwischenglühung durchgeführt, kann das Nachziehverhältnis auf etwa 1,6 gesteigert werden, was zu einem maximalen Länge-zu-Durchmesser-Verhältnis von etwa 9:1 führt.
Verfahrenskombination | h/d |
---|---|
1 x Tiefziehen & Abstreckgleitziehen | 3 / 1 |
2 x Tiefziehen & Abstreckgleitziehen | 4 / 1 |
3 x Tiefziehen & Abstreckgleitziehen | 5 / 1 |
2 x Tiefziehen & Glühen & Abstreckgleitziehen | 9 / 1 |
Tbl. 1 Höhe-zu-Durchmesserverhältnis |