Friction & Tribology
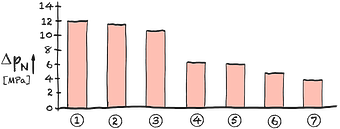
The tribological conditions during sheet metal forming can be influenced by various measures. A measure of the influence are the maximum achievable contact normal stresses in strip drawing tests. A favorable tribological system enables high contact normal stresses without cracks occurring. The topography of the sheet metal has the greatest influence, followed by the type and quantity of lubricant.23
The average coefficient of friction μ between the effective surfaces of the sheet metal and the tool is typically 0.05 to 0.20 and can therefore vary by a factor of 4.3 Since the coefficients of friction are usually included linearly in the equations for the forming forces, the high energetic importance of a favorable friction system quickly becomes clear.
Strip drawings with bending deflection tend to show higher coefficients of friction. Low sliding speeds mean higher coefficients of friction.23
Qualität | μ | Tribosystem | Blechtopografie | Blechfluss |
---|---|---|---|---|
Sehr Gut | 0.05 | TiC/TiN Schmierstoff ≥ 3 g/m2 VZ = 400 mm/s | EDT SBT | Eben |
Gut | 0.1 | Ziehfolie Polierte Oberfläche Ampco | EBT EDT LT SBT | Eben |
Mittel | 0.15 | Mittlere Beölung Werkzeug nicht poliert | EBT EDT LT SBT | Biegung |
Schlecht | 0.2 | Schmierstoff ≤ 1,5 g/m2 Werkzeug nicht poliert VZ = 25 mm/s | EBT | Biegung |
Tbl. 1 Average coefficients of friction for sheet metal forming323 |
The coefficient of friction μ is influenced by the following parameters:
- Lubricant & Viscosity
- tool material
- tool zone
- exposure time tool
- tool coating
- tool topography
- die geometry
- surface structure of the sheet metal
- draw speed
- surface pressure
- temperature
tool zone
In the forming zone, the coefficient of friction μ at die radius is significantly higher ( μ = 0.15 - 0.22) than under the flat blank holder (μ = 0.05 - 0.10) due to the additional bending.23
draw speed
Higher forming speeds VZ generally reduce friction, which is due to hydrodynamic effects.
tool geometry
Modern die radii (e.g. superellipse) can significantly reduce the maximum contact normal stresses that occur during deep drawing. This reduces sheet metal leveling and improves the flow of the lubricant into the forming zone.24
exposure time tool
Increasing tool wear levels the tool topography and leads to deterioration of the friction system. Frequent maintenance intervals can counteract this.
Lubricant Viscosity & Temperature
The viscosity of the oil is decisive for the coefficient of friction. A lubricant with a high viscosity can be held better in the forming zone by the topography than a low-viscosity one. If the tool warms up, the oil viscosity decreases.
surface pressure
The sheet metal can thicken due to tangential compressive stresses. Since the sheet metal holder is only supported locally, high contact normal stresses pN up to the yield point can occur. This leads to a leveling of the surface topology of the sheet metal and thus to a change in the coefficient of friction.
quantity of lubricant
The higher the quantity of lubricant, the lower the coefficients of friction. Depending on the difficulty of forming, more or less oil is applied to the sheets:
- 1.5 g/m 2 per side for easy reshaping
- 2 g / m 2 per side for medium forming
- 2.5 - 3 g/m 2 for difficult pressed parts, if necessary with partial additional lubrication
surface texture
A smooth sheet metal surface is unfavorable, as it is not possible to keep a sufficient quantity of lubricant between the sheet metal and the tool during difficult forming processes. As the most important topographic parameters, the fineness, the seclusion and the emptiness influence the friction behavior.23
The surface structures include:
- SBT shot blast texturing
- EDT Electrical Discharge Texturing
- LT Laser Texturing
- EBT Electron Beam Texturing