Warm forming stainless steel
Introduction
Process design for forming thin sheets made of stainless steel is a challenging task, as the selection of a suitable forming process is often limited based on parameters such as uniaxial tensile test, microstructure and chemical composition.
When exposed to mechanical stress, transformations of austenite into martensite can occur in austenitic, stainless materials with nickel contents < 11%, which can further change the mechanical properties. Studies have shown that this martensite transformation is particularly influenced by process parameters such as temperature, stress state and forming rate.34227071
The starting point for the experiment described here was a customer request: Residual stresses created on a stainless steel pot made it difficult to form the edge. We took this as an opportunity to examine two stainless steel variants in relation to the drawing process in order to minimize the resulting residual stresses by influencing the process parameters.
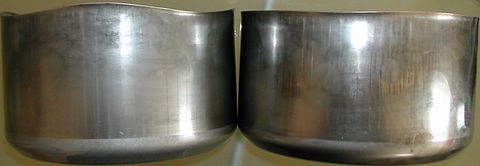
Nr. | Bezeichnung | Rp0,2 | Rm | A5 |
---|---|---|---|---|
1.4571 | X6CrNiMoTi17-12-2 | 215 | 500-730 | 50 |
1.4539 | X1NiCrMoCuN25-20-5 | 220 | 520 - 720 | 40 |
Tbl. 1 Test materials stainless steel |
task
As part of this project, we examined two types of stainless steel (table), both examples of austenitic stainless steels. The stainless steel 1.4539 is characterized by increased nickel and molybdenum content, which leads to increased resistance to stress corrosion cracking and improved resistance to pitting. Our goal was to deep-draw these two stainless steels and, in particular, to change the temperature process parameter in order to reduce the residual stresses that were created.
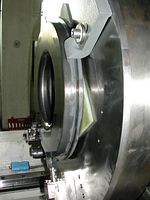
test execution
The forming task consisted of a single-stage deep-drawing process. A 4Ming brand quadruple-acting hydraulic press was available for this purpose. Two of the four force effects were switched off for the test. With regard to minimizing martensite formation , the optimal forming temperature of 80 °C has been adequately described.22 First, drawing tests were carried out at room temperature (approx. 25 °C). Then both the deep-drawing tool and the blank material were brought to the target temperature of 80 °C. In order to prevent it from cooling down too quickly, the active parts were covered with insulation boards. At the same time, the circuit boards were heated to the target temperature in an oil bath.
At the same time, the circuit boards were brought to the target temperature in an oil bath. A common lubricant for stainless steel forming (manufacturer Avia) was used as the lubricant.
The material for the tool was 1.2379, coated with a plasma gas nitriding layer. In order to counteract the thickening of the edge and the associated wrinkling in the inner area of the flange during the drawing process, the inlet gap on the blank holder side was designed to be 1/10 conical.
Parameter | Bezeichner | Wert | Einheit |
---|---|---|---|
Rondendurchmesser | D0 | 300 | mm |
Enddurchmesser | d1 | 160 | mm |
Ziehverhältnis | β | 1,88 | |
Blechdicke | s0 | 1 | mm |
Ziehgeschwindigkeit 1 | vZ 1 | 30 | mm/sek. |
Ziehgeschwindigkeit 2 | vZ 2 | 100 | mm/sek. |
Platinentemperatur 1 | t1 | 25 | °C |
Platinentemperatur 2 | t2 | 80 | °C |
Tbl. 2 Experimental parameters |
Results 1.4539
After reaching the target temperature of 80 °C for the blank holder, the drawing die and the blanks, we started with the warm drawing tests. Due to the change in viscosity, pronounced scoring developed after the first drawing process. In order to counteract this failure in the future, a higher-viscosity oil should be used.
The flag saw test provided qualitative information about the remaining residual stresses. The figure below shows the high-alloy 1.4539 formed at room temperature on the left and at 80 °C on the right. The remaining residual stresses in both pots are almost identical.
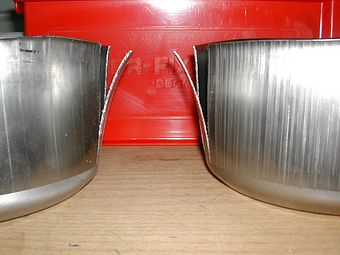
Results 1.4571
With stainless steel 1.4571, a significant reduction in internal stresses can be seen during warm forming in the sawing test. After warm forming, the magnetization of this stainless steel was no longer detectable.
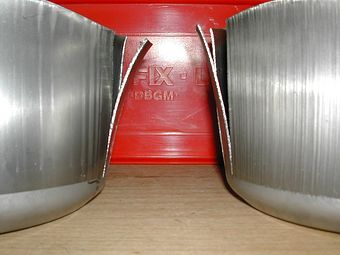
Conclusion
In a direct comparison of the two stainless steels, the tests show that similar residual stresses occur at room temperature, while the semi-hot formed pots show a significant reduction in residual stresses with 1.4571.
The reduction of residual stresses in metastable austenitic stainless steels due to heating of the tool and the blank is significant. In the future, the use of heat sources in the tool must be considered for similar tasks. In the case of multiple forming of rectangular parts in particular, targeted heating offers the potential to achieve higher degrees of forming.