Thermoforming & Injection Molding
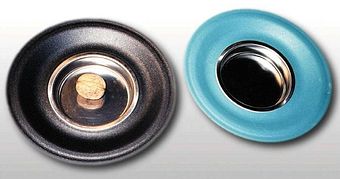
With the innovative combination of deep drawing and injection molding, made possible by a specialized injection molding machine and a two-stage compound tool developed by Arburg and the company 4Ming® in Bretten, combination products made of metal and plastic can be manufactured in a single operation. This method is particularly attractive to plastics processors who don't want to make the additional investment in a metalworking press and outsource the prefabrication to an outside provider.
In a specific example, a combination of deep drawing and injection molding tool is used to produce a shell. The deep-drawn part of the shell is made of stainless steel (1.4301) and is overmoulded with a plastic edge in a second step in the same tool.
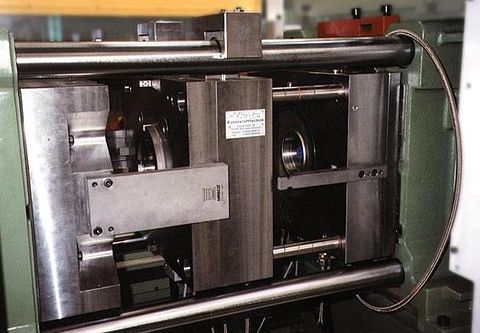
The way it works is as follows: During the closing movement, the two-stage tool forms the shell from a metal cylinder. An Arburg 3-axis NC handling system removes the shell from the deep-drawing area with suction cups on both sides.
In the injection molding area, the shell is then overmoulded with a plastic edge. Both processes therefore run simultaneously: with each cycle, a deep-drawn metal part and an overmolded finished part are created.
The machine is designed in such a way that the deep-drawing area of the mold is on the moving side and the injection mold is on the fixed clamping side. The opening and closing process of both levels of the mold is controlled via a latch lock in such a way that when the mold is closed, the injection molding area always closes in front of the thermoforming device. The forming process takes place mechanically using hydroelastic deep drawing. The blankholder is moved backwards by the closing movement of the tool and the drawing punch is moved forwards as a result. This stretches and compresses the material at the same time, transforming it into a hollow body. The injection molding area of the tool does not differ significantly from a conventional mold.