4Ming press for beer kegs in comparison
A comparison of the 4Ming ® press with a press line for beer barrels shows many advantages for the 4Ming press. The following can be summarized:
Disadvantages of the press line:
- The costs and payback periods are twice as high.
- A high connected load is required.
- High ongoing energy costs.
- The sound pressure level is high.
- A foundation is necessary, which makes the system immobile.
- The press height requires a high hall.
- A long tool change time is required.
- The installation is complex.
- An oil mist extraction system is required.
Advantages of the 4Ming ® press:
- The investment costs are approximately half of those for a press line.
- A lower connected load is required.
- Much lower energy costs.
- Low sound pressure level.
- No foundation necessary, the system can be moved.
- No high hall required.
- Short tool change times.
Cost comparison 4Ming press and press line for slim beer barrels
Position | Pressenlinie [€] | 4Ming Presse [€] |
---|---|---|
Ziehpresse 1 | 733,000 | 700.000 |
Ziehpresse 2 | 590,000 | entfällt |
Rondenentstapelung & Befettung & Transfersystem | 534,000 | 300.000 |
Anlagen-Leitsteuerung | 56,000 | integriert |
Ziehwerkzeug 1. Zug | 112,000 | 100.000 |
Ziehwerkzeug 2. Zug | 92,000 | entfällt |
Aufstellung & Erprobung bei Hersteller | 79,000 | 79.000 |
Montage & Inbetriebnahme bei Kunden | 162,000 | 100.000 |
Fundamentkosten | 100,000 | entfällt |
Gesamtinvestition | 2,458,000 | 1.279.000 |
Tbl. 1 Cost comparison press line with 4Ming ® press for slim beer barrels |
Press line for slim beer kegs
A production line for slim beer kegs requires two drawing presses. The blank sizes vary between 400 and 600 mm and the blank thickness is between 1.5 and 1.9 mm stainless steel. As a rule, a stack of blanks has a height of between 100 and 500 mm.
Production is around 6 parts per minute in three shifts. The cycle time of the presses from start to finish is approximately 6 seconds and the automation time is 4 seconds for a total cycle time of 10 seconds.
The associated transfer has a feed path of 1,200 mm and a lowering and lifting stroke of 60 mm.
The maximum height of the drawing press is 6 meters and a foundation depth of around 1.6 meters is required.
The total installed connected load is 400 kW.
The maximum sound pressure level of this system is 83 dB(A).
The first drawing press has a total force of 4,000 kN with a die cushion force of 2,000 kN. The second drawing press for the final drawing has a total pressing force of 1,600 kN and a die cushion force of 400 kN.
The hydraulic unit requires water cooling and the spray lubrication requires suction.
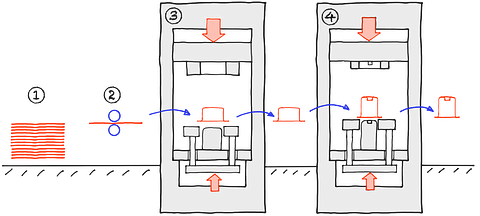
4Ming press for slim beer barrels
To produce slim beer kegs, a 4Ming press only requires a horizontally aligned, triple-acting press. It is able to process boards with a diameter of 400 to 600 mm and a thickness of between 1.5 mm and 1.9 mm.
Production is approximately 6 parts per minute in three shifts. The press cycle time from start to finish is approximately 7 seconds, while the automation time is 3 seconds, giving a total cycle time of 10 seconds.
A gripper transfer is not necessary, as servo axis automation instead transports the board from the stack into the oiling and then into the press.
The maximum system height is only 2.5 m and a foundation is not required.
The total installed connected load is only 200 kW.
The maximum sound pressure level of this system is less than 75 dB(A).
The triple-acting drawing press has a total force of 4,000 kN.
In addition, water cooling is not necessary for the hydraulic unit, nor is suction required for lubrication.
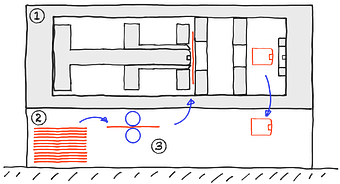