4Ming Press Productivity
The productivity of a production process depends largely on the cycle time. Reducing this time consequently increases productivity. Below the productivity of the 4Ming press is compared with the productivity of a single press.
1) Single press
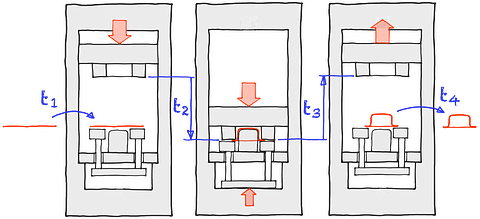
The cycle time of a single press is determined by the following individual times:
- Time to load t1
- Forming time t2
- demolding time t3
- Removal time t4
- tool set-up time tr
- Other times to set up the workplace
The forming and demolding times are determined by the press speed. In general, the press moves at a rapid traverse speed unless it is in contact with the sheet metal. Depending on the application, the forming speed is between 50 and 150 mm/sec. In the case of high drawn parts, the demoulding speed should not be significantly higher in order to ensure that the drawn part can be stripped off without any problems. Depending on the type of press, the rapid traverse speed can be between 200 and 400 mm/s.
The analysis and optimization of these factors contribute to increasing productivity. With the 4Ming press and its sophisticated processes, an efficient balance of these times can be achieved, which makes it a particularly productive solution.
2) 4Ming press
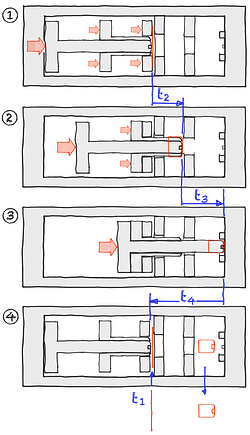
The 4Ming ® press is characterized by its characteristic longer strokes, which, however, have a positive effect on the press occupancy times. A significant advantage of this press is its efficiency: the demoulding of the respective trains takes place parallel to the forming of the following train, which eliminates unnecessary idle strokes for removing and loading the individual stations.
This parallel processing means that the loading of boards and the removal of components can be carried out simultaneously. This leads to a significant reduction in cycle time compared to conventional individual presses.
The 4Ming press also offers the advantage that the entire composite tool only needs to be replaced once. In contrast, a single press requires setup for each individual operation. Overall, the 4Ming press enables more efficient use of the press capacity.
productivity
Assuming the same press speeds, the 4Ming ® press proves to be significantly more productive. This advantage arises from the fact that there is no need for repeated setup. In addition, the loading of the blank and the removal of parts is parallelized - a process that is not possible with individual presses and press lines due to the system.
It becomes clear that the more drawing stages are carried out, the more significant the productivity advantage is.
Umformstufen | Belegungszeit Einzelpresse [s] | Belegungszeit 4Ming Presse [s] | Produktivitäts Verhältnis |
---|---|---|---|
Einstufiges Ziehen der Hauptform | 23 | 10.9 | 2.1 |
Einstufiges Ziehen der Hauptform & Nebenform | 46 | 11.9 | 3.9 |
Zweistufiges Ziehen der Hauptform & Nebenform | 67.6 | 15.4 | 4.4 |
Dreistufiges Ziehen der Hauptform & Nebenform | 88.2 | 17.8 | 5 |
Tbl. 1 Press occupancy times & productivity ratio 4Ming ® press to individual press |