Bleche & Ziehteile Penetrieren
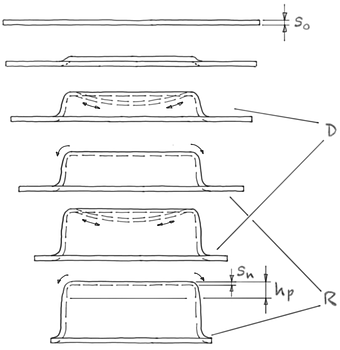
Das Penetrieren bietet die Möglichkeit, Verfestigungen im Ziehteilboden gemäß den spezifischen funktionalen Anforderungen des Ziehteils anzupassen. Durch wiederholte Deformation und erneute Formung der Bodenfläche erfolgt eine Materialumverteilung vom Boden in die Wand des Ziehteils. Diese Methode steigert die Materialeffizienz und erhöht somit die Nachhaltigkeit des gesamten Fertigungsprozesses.*****
Während der Deformationsphasen wird die Oberfläche der Bodenfläche vergrößert, was zu einer Reduzierung der Blechdicke in diesem Bereich führt. In den anschließenden Reformationsphasen fließt Material vom Boden in die Wand des Ziehteils. Diese Umverteilung des Materials bedeutet, dass bei einer gleichbleibenden Ziehteilhöhe eine kleinere Ausgangsplatine verwendet werden kann.
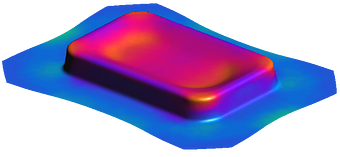
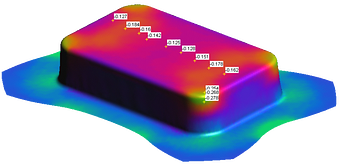
Nach mehreren Penetrationen folgt eine Bodenausdünnung zwischen 12 - 18 %. Die Einsatzplatine kann entsprechend verkleinert werden.
Die Vorteile dieses Verfahrens umfassen:
- Verfestigung Ziehteilboden bis zur maximale Dehnungsmöglichkeit des Bleches
- Erreichung eines höheren Umformgrads
- Verstellbare Eigenschaften durch variable Parameter
- Bedeutende Materialeinsparung*
- Möglichkeit der Prozessregelung
- Verbesserung der Formhaltigkeit
- Erhöhung der Prozessstabilität
- Reduzierung der Ausschussquote
Die Umstellung eines bestehenden Prozesses auf dieses Verfahren kann in vier Schritten erfolgen:
- Durch eine erste Machbarkeits- und Wirtschaftlichkeitsanalyse lässt sich das Potenzial des Verfahrens abschätzen.
- Ermittlung der Materialeinsparung und Formgenauigkeit durch vergleichende
- Herstellung einer Testplatine auf einer Testpresse. Diese Testplatine wird durch den bestehenden Prozess geführt, und die daraus resultierenden Eigenschaften können evaluiert werden.
- Im letzten Schritt wird die Umstellung des Prozesses geplant und umgesetzt.
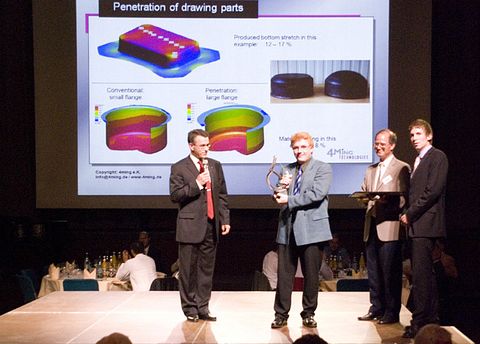
Diese Technologie wurde im Rahmen der Internationalen Konferenz "Neuere Entwicklungen in der Blechumformung 2008", organisiert vom IFU Stuttgart unter der Leitung von Herrn Prof. Dr.-Ing. Liewald MBA, mit dem Wissenschaftspreis geehrt.