Punch compression & tension stress
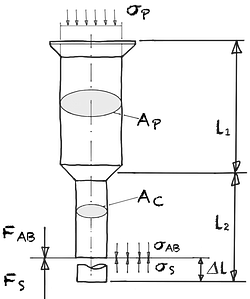
The forces acting on the cutting punch can lead to various compressive and tensile loads. It is important to check the acceptability of these loads.
For safety reasons, the calculation of the pressure surface of the punch head does not use the outside diameter of the punch head, but the diameter of the shank.
If the punch pressure exceeds 1,200 MPa, low-alloy tool steels are no longer suitable for the punch material. In such a case, you should use a high-alloy tool steel, or even better, a high-speed steel.25
If the shaft pressure is over 200MPa, there is a risk that the punch will dig into the soft top plate. To prevent this, a hardened pressure plate (eg made of material 1.2842) should be used between the punch holding plate and the base plate. The Rockwell hardness of this plate should be 58 HRC, since too hard pressure plates can lead to breakouts on the punch heads.512532
Cutting Pressure | σS | = | MPa | ||
Shaft Pressure | σP | = | MPa | ||
Stripper Tensile Stress | σAB | = | MPa | ||
Elongation | Δl | = | mm |
Cutting power | FS | = | kN | |||
Stripper force | Fab | = | kN | |||
Cutting face | AC | = | mm2 | |||
Shaft area | AP | = | mm2 | |||
Length | l1 | = | mm | |||
Length | l2 | = | mm |
Example I A stepped punch with a cutting face of 78.5 mm 2 (round punch 10 mm) and a shaft area of 314 mm 2 (shank diameter 20 mm) is subjected to a cutting force of 39.4 kN. The stripper force is thus 11.8 kN, the cutting pressure is 502 MPa, the shank pressure is 126 MPa and the stripping tensile stress is 150 MPa.