Compensation for spring back
In the production of rigid sheets, beading structures are created using embossing. This can cause springback as well as the undesirable phenomenon of buckling. This phenomenon is also colloquially referred to as “folding over the corner” or “frog”.55
The phenomenon described can occur in the form of a bifurcation. This means that by applying a small external force, several stable end positions of the sheet are possible.
The following parameters are crucial as an influence on spring back
material
The higher the strength, the higher the spring back
number of beads
The smaller the uninfiltrated area, the lower the spring back
beading depth
The beading depth linearly increases the spring back
die radius hardly changes the spring back
The following strategies can reduce spring back :
- Optimization of the bead arrangement
- Low beading depth
- Compensation through counterpressure
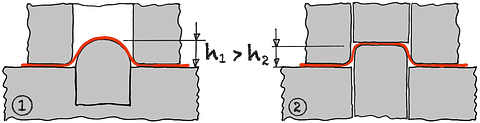
Compensation by back pressure
In the case of channel-like beads, the embossing stamp is often designed in the hemispherical. The tensile stresses that arise in the bead flanks can be partially compensated by leveling the bead in a subsequent work step. As a result, the tensile stresses in the flanks are superimposed by compressive stresses , which leads to a significant improvement in stability of up to 80%. In addition, the component is then in a stable state. A disadvantage is that reducing the bead depth noticeably reduces the section modulus. In addition, an additional operation is necessary.
With a multiple-acting tool structure, this post-forming can also be carried out in just one operation, which, however, makes the tool more complicated