The 4Ming Press: Innovation in Sheet Metal Deep Drawing
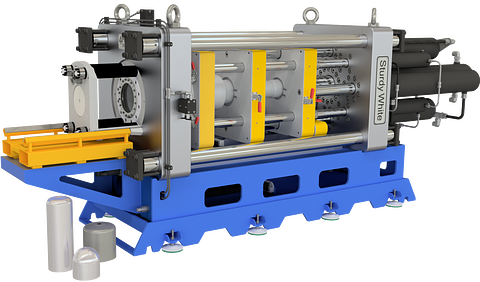
The 4Ming® press is a specialized machine designed for deep drawing of sheet metal for the production of high drawn parts. The sequential drawing process allows several drawing and stamping steps to be carried out in one operation. The drawn parts produced are used in a variety of products including air tanks, beer kegs, pressure vessels and funeral urns. The 4Ming® press represents a key technology in modern production and offers innovative solutions for the industry.
Forming Stages and Productivity
The 4Ming® press allows up to three stages of drawing for the main shape as well as the final punching of holes or collars. Compared to conventional individual presses, the 4Ming® press significantly reduces the occupancy time because there is no changeover required. The occupancy time is 20% compared to a single press, which corresponds to five times the productivity. This increase enables faster and more economical production of drawn parts.
Energy and Material Efficiency
By using a variable-speed displacement control on all four hydraulic axes, energy is only consumed during the forming phase. There is no lossy energy turnover during the standstill phase. Compared to resistance control, the energy requirement is reduced by more than 70%.
A special movement kinematics of the actuators enables the sheet metal to be redistributed from the bottom of the drawn part to the frame, which means that the board can be made up to 10% smaller. For this innovation, 4Ming® was awarded the University of Stuttgart Science Prize.1
Tool Change
The tool change on the 4Ming® press is carried out using a high-lift truck and only takes 20 minutes. This fast and efficient method allows the machine to be used in various production environments, including small series, series and assembly lines.
Automation and Cost Comparison
The associated automation of the 4Ming® press includes blank destacking, oiling and round blank, with a loading time of less than 2 seconds. If heated immersion oiling is used, an annealing process can be saved when forming stainless steel.
Compared to a three-stage press line with associated automation, the 4Ming® press is around a third of the cost with the same output.