Structure optimization
In structural optimization, mechanically or thermally stressed components are optimized or improved in terms of their shape. In this process, draft or design variables are defined that are iteratively improved in relation to the desired goal according to specific optimization algorithms. 76 75
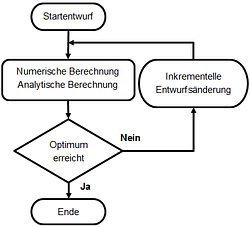
Starting from a starting design, analytical and/or numerical calculations are carried out. The subsequent evaluation determines whether the optimum has been achieved. If not, an incremental change to the design is made, followed by another calculation cycle. Reaching the optimum ends the process. The task of the optimization algorithms is to increase the efficiency of finding solutions. Depending on the design variables, different disciplines of optimization are distinguished.
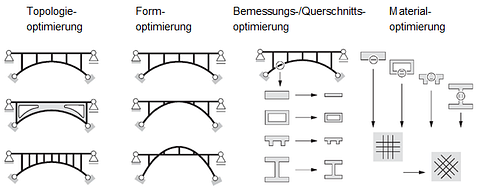
Topology Optimization : This involves distributing the mass in a given space. The design variables here are the density and accordingly the distribution of the modulus of elasticity in space.
Shape Optimization : For a given component topology, the shape is improved.
Design Optimization : For fixed shapes, this discipline affects the cross-sectional dimensions or thicknesses.
Material optimization : The material structure used is influenced here. This can be, for example, fiber alignment or layer thicknesses in composite materials.