Mode of operation drawing presses
The drive of deep-drawing presses is decisive for the energy consumption. Different types must be distinguished:
- Single or double acting press
- Active counter-pull
- Deep drawing with transmission gear
- Mechanical or hydraulic press
Depending on the arrangement of the drives, there are differences in the use of energy and in the resulting drawn position.
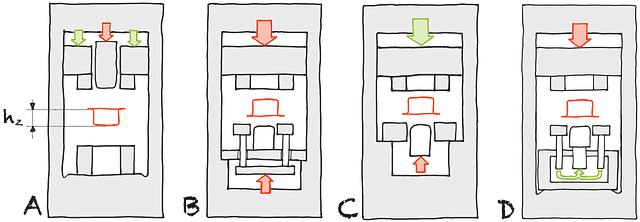
A) A drawing ram and a separate blankholder ram are both actuated from above.68 This production in flat position often requires a complex turning station, since the component has to be turned for a subsequent cutting and embossing station.
If the blank is firmly clamped by the blank holder using a pressure-maintaining pump, the blank holder does not perform a stroke during forming and the blank holder work is low. The following parameters are used to determine the drawing work:
Press stroke under load hp = hz
B) The force effect for holding the sheet metal is achieved by a pulling device in the press table. Due to the hat position production, there is no need for a turning station.
This mode of operation is energetically unfavorable. The sheet metal holder moves over the drawing stroke and press power is converted into thermal energy while the hydraulic drawing device is controlled. The resulting heat must be removed from the system through complex cooling. The characteristic values for mode of action B result from:
Press stroke under load h p = h z = h nh
C) The blank holder ram acts from above and remains still during forming. The drawing punch actively carries out the forming stroke from below. The sheet metal holder does not contribute energetically to the balance.
The reduced energy requirement compared to the single-acting press and the production in the hat position are advantageous. The characteristics are the same as A with:
Press stroke under load hp = hz
D) The downward movement of the press ram is translated into an upward movement of the drawing punch. The blank holder force adjusts itself automatically by converting the punch force into the blank holder force using the selected transmission ratio. One of its properties is the increase in drawing speed. This leads to an additional increase in output, especially in the case of mechanical presses with several stations.65 For the calculation of the forming energy, favorable characteristic values result with:
Press stroke under load hp = 1/2 x hz = hnh
In summary, it can be stated that the mode of operation and the structure of drawing presses have a decisive influence on energy consumption. It is therefore important to fully understand the requirements of the specific forming process and to select the most appropriate press configuration.