Cutting length & bending shortening
During the bending process, the material in the bending zone is stretched and thus plastically deformed. Since the material is considered incompressible, it must be moved from the compressed to the stretched side. Therefore, the blank sheet metal part (circuit board) must be shortened accordingly before bending. This correction of the length is referred to as bending shortening Δl0.
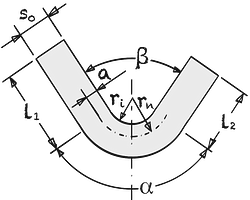
The neutral fiber describes a layer of the material that is neither compressed nor stretched during the bending process. It is important to note that this neutral line does not always run right down the middle of the material. In fact, with a smaller inner radius ri , it migrates more inwards, which leads to a reduction in the original cutting length l0.25
Cutting length | l0 | = | mm | ||
Radius, neutral axis | rn | = | mm | ||
Correction value | K | = | |||
Bending deduction | Δl0 | = | mm |
Leg length | l1 | = | mm | |||
Leg length | l2 | = | mm | |||
Bending angle | α | = | ° | |||
Inner radius | ri | = | mm | |||
Sheet thickness | s0 | = | mm |
The exact bend deduction is difficult to predict because a variety of parameters affect it to varying degrees:
- strength of the material
- ductility of the material
- structure of the material
- grain size of the material
- sheet metal thickness
- Anisotropy (dependence of properties on direction, especially in relation to the orientation of bending to the rolling direction)
- Bending processes (such as die bending, free bending, swivel bending)
- Surface roughness (both the sheet and the tool)
- Lubricant used
- Existing coating
- bending angle
The thickness of the sheet ( s0 ) is reduced in the bending zone by around 10 to 20%, depending on the bending radius and the material used. With a very small radius (almost sharp-edged tool), the thickness of the material can decrease even more.