Spring back
During the bending process ① an elastic-plastic load occurs. When the workpiece is then unloaded ②, the remaining internal stresses in the cross section lead to a restoring moment, which causes the workpiece to spring back.
Elastic spring back is a central phenomenon when bending workpieces and plays a crucial role in the planning and execution of bending processes. To achieve the desired end product, it is essential to accurately predict the effects of elastic spring back and compensate accordingly. This can be achieved either through initial excessive bending or through an adjusted post-bending process.
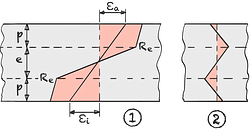
The phenomenon of spring back is a ubiquitous factor in all bending processes and must be taken into account for precise and error-free execution of the process. In order to ensure effective compensation for spring back , it is essential to precisely calculate the springback angle or radius in advance and incorporate it into the bending process.
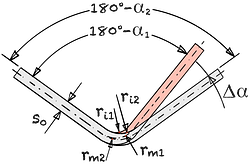
Springback factor | k | = | |||
Bending factor | c | = | |||
Inner radius | ri1 | = | mm | ||
Bending angle | α1 | = | ° | ||
Change angle | Δα | = | ° |
Yield strength | Rp 0,2 | = | MPa | |||
Young's modulus | E | = | GPa | |||
Workpiece inner radius | ri2 | = | mm | |||
Sheet thickness | s0 | = | mm | |||
Workpiece angle | α2 | = | ° |
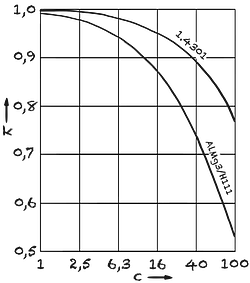
Leaving the bending punch in the bending die for a longer period of time does not change the springback behavior. By pressing further, a reduction in spring back can be achieved via the follow-up effect.8